High-Frequency Welded Fin Tube Supplier
A type of heat exchanger component where fins are attached to a base tube using a high-frequency welding process.
Professional High-Frequency Welded Fin Tube Manufacturer
Cufin Tube’s high-frequency welded fin tubes are specialized components designed for efficient heat transfer in various industrial applications. These tubes are characterized by fins that are spirally wound around a base tube and welded using high-frequency welding techniques, resulting in a robust bond that enhances performance under mechanical stress.
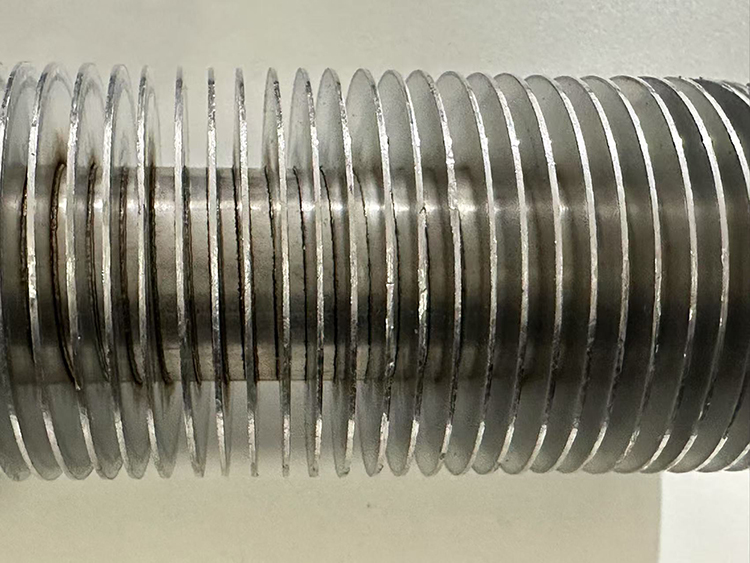
Technical Specification:
- Fin Height: Ranges from 6 mm to 50 mm;
- Fin Thickness: Typically between 0.3 mm and 3.5 mm;
- Operating Temperature Range: Up to 600°C (1112°F), depending on material and designFin Types: Solid fins, Serrated fins, U-type and L-type fins
- Outer Diameter: Typically ranges from 15.88 mm to 273 mm (0.625″ to 10″)
Main Application:
High-frequency welded fin tubes are suitable for a variety of applications such as heat Recovery Systems, power generation, chemical metallurgy and cement Industries,etc. The versatility and efficiency of high-frequency welded fin tubes make them essential in sectors that require effective heat management solutions.
High-frequency welded fin tubes Technical Specification
Parameter | Specification Range |
---|---|
Base Tube Material | Carbon Steel, Alloy Steel, Stainless Steel, Duplex Stainless Steel, Inconel, Titanium |
Base Tube Thickness | 2.0 mm and above |
Fin Height | 6 mm to 50 mm |
Fin Thickness | 0.3 mm to 3.5 mm |
Fin Type | Solid fins, Serrated fins, U-type, L-type |
Fin Density | Varies as per customer requirements (e.g., 2 to 7 fins per inch) |
Operating Temperature | Up to 600°C |
Welding Process | High-frequency electric resistance welding |
What is High-frequency welded fin tubes?
High-frequency welded fin tubes are specialized heat exchange components designed to enhance thermal efficiency in various industrial applications. They consist of a base tube with fins welded onto its surface using a high-frequency electric resistance welding process. This method ensures a strong bond between the fins and the tube, optimizing heat transfer while maintaining structural integrity.
- Welding Process: The fins are attached to the base tube using high-frequency electrical resistance, which allows for precise and efficient welding without the need for filler materials.
- Material Options: These tubes can be made from various materials, including carbon steel, stainless steel, and alloys, making them suitable for different operating conditions.
- Design Flexibility: Available in various fin heights, thicknesses, and configurations (solid, serrated, or U-type), allowing customization based on specific application needs.
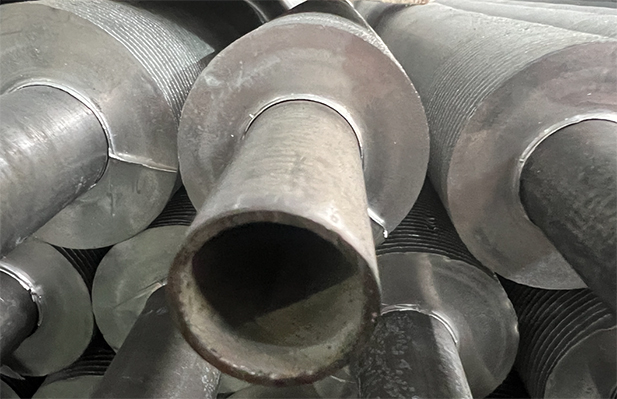
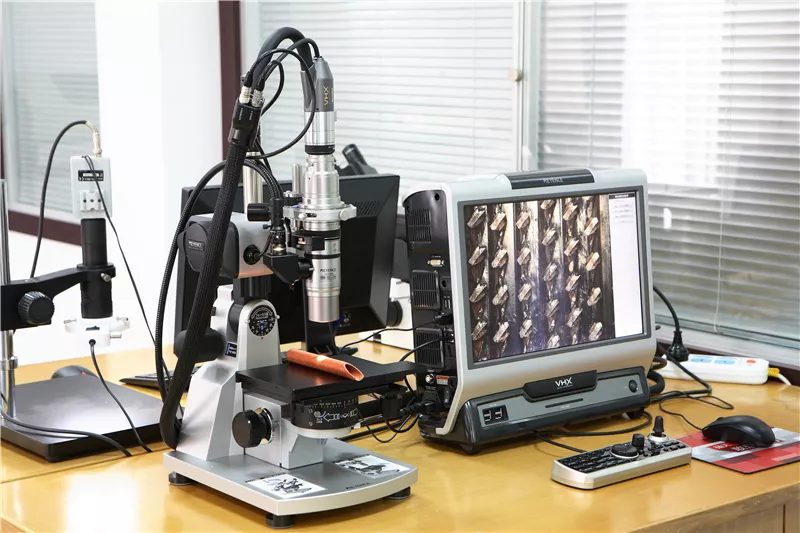
Advantages Of High-frequency Welded Fin Tubes
High Temperature Capability : High-frequency welded fin tubes can operate effectively at elevated temperatures, often up to 600°C, making them ideal for high-temperature applications like boilers and furnaces.
Enhanced Heat Transfer Efficiency: Increased Surface Area: The fins increase the surface area available for heat exchange, significantly improving thermal performance compared to bare tubes.
Minimized Thermal Resistance: The continuous welding process ensures a strong bond between the fins and the tube, reducing contact thermal resistance.
How do High-frequency welded fin tubes work?
High-frequency welded fin tubes work by leveraging advanced welding techniques and innovative designs to maximize heat transfer efficiency. Their robust construction and adaptability make them invaluable in various industrial applications where effective thermal management is crucial.
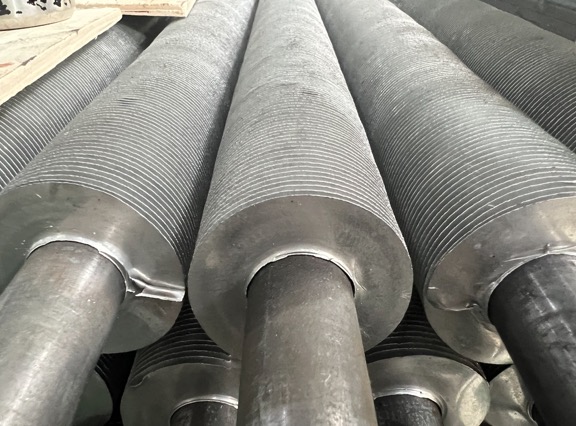
Applications Of High-frequency welded fin tubes
High-frequency welded fin tubes are widely used in industries such as:
- Boiler Economizers: Used to recover waste heat from flue gases, improving overall boiler efficiency.
- Air Preheaters: Employed to heat incoming air before it enters combustion chambers, enhancing fuel efficiency and reducing emissions.
- Heat Exchangers: Integral in reactors and other heat exchange systems where efficient thermal management is crucial.
- Process Heating: Utilized in various chemical processes that require precise temperature control.
Other Applications Including :
- Air Coolers
- Chillers
- Industrial Applications
- Heat Recovery Steam Generators (HRSG)
- Gas Coolers
- Heat Recovery Systems
- Heat Exchangers on Ships
- Cooling Systems for Offshore Platforms
- Waste Heat Recovery
- Pasteurizers and Sterilizers
Book A Video Call
Your reliable China partner of finned tubes for heat exchangers
Mass Production Photos
Check how we will produce your finned tube bulk orders in our future cooperation. We take every step seriously, from raw material to packaging, to ensure that the fin tubs delivered to your warehouse are 100% qualified.
Frequently Asked Questions
About High-frequency Welded Fin Tubes For Heat Exchangers
What is the corrosion resistance of high-frequency welded fin tubes?
The corrosion resistance depends on the material used. For example, stainless steel and alloy materials provide good corrosion resistance. For particularly harsh environments, special coatings can be chosen to enhance corrosion resistance.
What is the working principle of high-frequency welded fin tubes?
What is the maximum temperature they can withstand?
These tubes can typically operate at temperatures up to 600°C, depending on the materials used.
How do I choose the right high-frequency welded fin tubes?
What are the maintenance requirements for these tubes?
Regular inspections and cleaning are typically required to ensure optimal performance, with frequency depending on the operating environment.
What advantages do they have over other heat exchangers?
They offer higher heat exchange efficiency, greater mechanical strength, and better high-temperature resistance, making them suitable for extreme conditions.
Can these tubes be customized?
Yes, they can be customized in terms of fin height, thickness, and design to meet specific application requirements.
How is product quality ensured?
Product quality is ensured through strict quality control processes, including material inspection, welding tests, and final product inspections to meet industry standards.
Request A Free Quote
We'd like to work with you
Send us a message if you have any question or request a quote. Our expert will response within 24 hours and help you custom your finned tubes heat exchanger solution!